Saving Cool Cash on Hot Days
Academic partnership improves bottom line and green energy use
Quick Summary
- Engineers, staff, students, academic and consulting partners helped create an algorithm and user-friendly interface to optimize how our cooling system operates.
- The innovation improved our green energy use and, in its first year of implementation, saved $150,000+ in electricity charges.
- Three graduate students gained hands-on experience resulting in published research for them all and a Master's thesis for one.
UC Davis' Journey to Net-Zero
David Trombly, senior engineer supervisor with UC Davis Facilities Management and Ahmet Palazoglu, chemical engineering professor, discuss the chilled water optimization project and its cost- and energy-saving impact. Camille Kirk, sustainability planner and director of UC Davis Sustainability and Kiernan Salmon, product manager with UC Davis Facilities Management, highlight additional sustainability-related goals and projects.
Watch this video to learn more
(Note: This video was created by an outside company to show how UC Davis uses its platform to improve energy efficiency.)
Can we optimize how we cool our buildings without compromising campus comfort?
This question, the focus of a long-standing partnership between UC Davis Facilities Management and UC Davis Chemical Engineering (Process Systems Engineering), has resulted in savings, greener energy use and published research.
“Our campus cooling infrastructure is much more complicated than HVAC systems many use at their homes,” said David Trombly, a senior engineer supervisor at Facilities Management, who oversaw this initiative.
In most of our campus buildings, the chilled water responsible for cooling the air that beats back the Davis heat originates at the campus's Central Heating and Cooling Plant. There, chillers use electricity to cool water to 40 degrees. When the temperature is right, the water can be (A), sent directly to buildings; (B), directed to our own thermal energy storage tank (a large container capable of storing 5 million gallons of chilled water); or (C), delivered from the storage tank to our buildings.
Prior to this academic partnership, the rationale used by plant operators deciding between these three choices varied. Now, an algorithm optimizes the timing for taking each of these actions. In its first year of implementation, the partnership saved our campus $150,000 (8-10 percent of our total cooling cost) and afforded our university a way to increase the energy we use from sustainable sources, like solar and wind.
Deep Dive
How we optimized for cheaper, greener electricity
The first piece of the optimization puzzle was electricity prices. The team had to be sure they had a complete and detailed understanding of how campus is charged for electricity.
“In order to learn all the intricacies of our electricity rates, I had to ask a lot of questions and even take a field trip to the campus electricity provider,” Trombly said. He was joined in this effort by Devon Schmidt, a graduate student in the Energy Graduate Group, who ultimately wrote her Master’s thesis based on the project. They returned with a clearer picture of how campus electricity rates fluctuate, not only from day to day, but throughout the day.
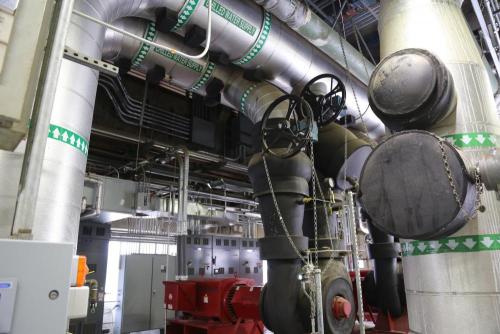
“Once we understood it, we could use the price fluctuation to our advantage,” Trombly said. “We could fill the storage tank during periods with lower prices and then use the tank, instead of water chillers, during periods with higher prices — strategically shifting our electricity load.”
This “load shifting” strategy based on electricity rates also allows the chillers to use cleaner, renewable sources of energy more often.
“High electricity prices are caused by high demand. When demand is high, then older, more inefficient plants supplement electricity with energy gained by burning fossil fuels,” Trombly explains. “In contrast, during lower-price periods, electricity is typically being supplied through greener sources, like solar and wind.”
Identifying all the variables – weather, prices, human operators
Using the price data, Ahmet Palazoglu and Nael El-Farra, professors in chemical engineering, and Gustavo Campos, their Ph.D. student, worked alongside Facilities Management to construct an optimization algorithm. In addition to day-of, day-ahead and extrapolated electricity rates, the algorithm factors in more puzzle pieces, including current and forecasted weather and demand for cooling. These forecasts were developed with Dan Colvin, a data scientist in Facilities Management.
“Weather impacts how the chillers run and building demand, which determines how much chilled water is needed, a hard constraint we always need to meet,” Palazoglu said. “The algorithm uses mathematical models to mimic how the system responds to input changes to determine which chillers to run, when to fill the tank and when to discharge the tank.”
One of the beauties of being on a campus like this ... it opens up opportunities for practical application.
-Professor Ahmet Palazoglu
Campos collaborated with the rest of the chilled water optimization team to write a research article about the development of the algorithm, which was published in Applied Energy, a highly-cited journal. In addition to publishing an article which corresponded with his existing research, Campos had the opportunity to gain experience working with clients and actually implementing his work.
“This partnership has been tremendously beneficial, providing one of our grad students with substantial practical application to prove methodology. Real life has unknowns. It doesn’t work like simulations.” Palazoglu said.
“One of the beauties of being on a campus like this — for many disciplines, it opens up opportunities for practical application. We’re grateful for the willingness of Facilities Management to be open to collaborate and take advantage of UC Davis as a research university."
Keeping it practical
Creating an algorithm would have been impossible without assistance from the staff at the heating and cooling plants. Plant operators and controls engineers manage all the systems that keep you from getting too chilly or too hot in your office, lecture hall or favorite study nook.
“By collaborating with the people who actually run the chillers and storage tank, we were able to figure out what was feasible from an operational perspective,” said Joe Yonkoski, a chemical engineer with Facilities Management who worked directly with staff members at the heating and cooling plants.
The insight gained from this close collaboration with operators allowed the team to identify operational constraints and keep the model practical for day-to-day implementation.
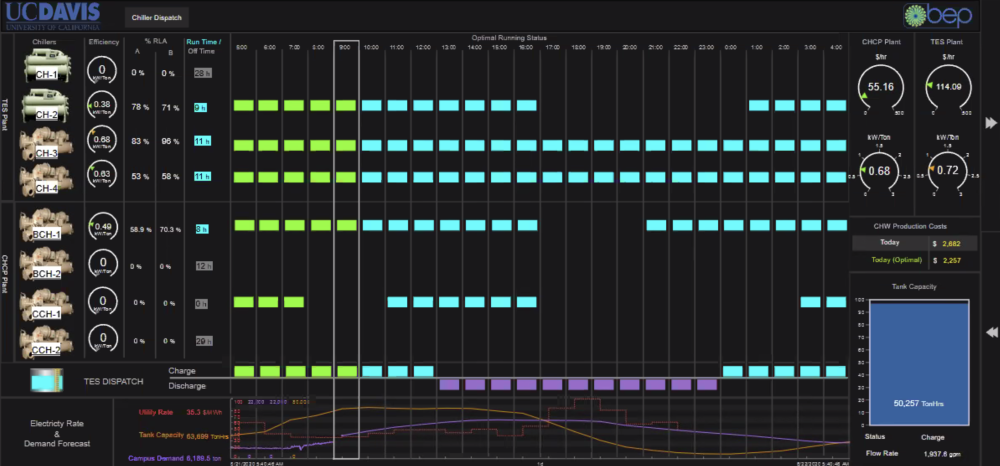
In order to implement the optimization model, the team created a user interface to guide operators at the heating and cooling plants. This process was done in collaboration with consultants from Smith Engineering, who worked closely with operators to ensure the algorithm and product worked well with operational constraints. The interface displays recommendations for what time to run each of the eight chillers, along with when to fill and when to dispatch the storage tank, determined by the algorithm.
“Before the project, operators would decide what chillers to run, when to run them, and when to use the thermal energy storage tank based on their general knowledge and assumptions of demand, electricity rates and equipment efficiency,” said Janice Stires, a project manager who has been working at the central plant for 18 years. “The interface simplifies the process by showing recommendations based on more specific and accurate information, making life a little bit easier and operations more consistent.”
However, operators still have the flexibility to use their own judgment.
“If there’s some sort of equipment failure not accounted for in the algorithm, then the operators can adapt,” Yonkoski said. “Similarly, while buildings were at low occupancy because of the pandemic, the optimization model, which is based on pre-COVID-19 data, didn’t accurately reflect campus demand. The operators used their experience to better suit campus needs.”
Once the final pieces were in place, the collaboration yielded benefits for all involved: Published research co-authorship for students, faculty and Facilities Management engineering staff; a new tool for informed and timely decision making by operators at our heating and cooling plants; electricity sourced from renewables for our campus community members; and, savings for funding future energy-saving projects.